WHAT SETS BRENNAN JACOBS INC APART FROM THE COMPETITION?
Brennan Jacobs’s factory trained personal and the equipment we use provided by NDT Technologies are what sets the company apart.
We use a system that was designed here in the United States by Herbert R. Weischedel, Dr.Ing., MSEE, P.E. and is manufactured here in the United States by Mr. Weischedel’s company NDT Technologies. Read more about his design and system here.
Wire ropes provide a lifeline for industry, often under hostile and demanding conditions. Frequently human survival is at stake, and acceptance of second-rate maintenance and inspection procedures is a risk that nobody should – and can afford to – take.
Better Magnetic Rope Testing Uses High Resolution and Noise Free Signals
Wire ropes are complex machines with a great many moving parts. They require attention, skilled operators, careful maintenance, inspection and lubrication.
In spite of their vital importance, wire ropes are frequently treated as and considered low-tech commodities. Failures are frequently accepted as “inevitable.”
With the appropriate inspections, wire rope failures can be predicted, and expenses and losses reduced. Consider that the price tag of rope failures can easily be in the seven or even eight digit range, and the cost of an inspection is marginal.
Much more dependable than visual inspections, magnetic rope testing (MRT) is a reliable non-destructive evaluation/examination (NDE) procedure used for the in-service inspection of wire ropes. NDE methods allow the detection and evaluation of external as well as internal rope deterioration. This allows the inspection of a rope’s entire cross-section to the core. MRT drastically increases wire rope safety. At the same time, it promises significant annual savings.
Ropes usually degrade internally with no visible indications. Internal deterioration modes include inter-strand nicking that will eventually develop into clusters of internal broken wires and corrosion including corrosion pitting.
External deterioration includes winding-on-drum damage. Urgently needed, suitable inspection equipment and procedures are now available – especially for the quantitative characterization of internal rope deterioration.

The Capabilities of New Generation NDE Equipment Include:
A dependable and consistent relationship between the condition of wire rope and NDE results. Noise free high-fidelity signals that allow the accurate measurement of a rope’s loss of metallic cross-section caused, for example, by corrosion and wear.
Reliable detection and quantitative characterization (measurement) of rope deterioration such as Inter-strand nicking, internal clusters of broken wires, internal corrosion including corrosion pitting.
Rope retirement standards that are geared to wire rope NDE can be developed and specified. These discard criteria will be based on quantitative defect characterization,Test data interpretation that is readily understood, and can be rationally explained and communicated.
Our instrumentation can dependably inspect rotation-resistant and non-rotating multi-strand and IWRC ropes, an important category of ropes that includes most crane ropes.
These ropes usually develop – and fail from – internal deterioration such as inter-strand nicking and clusters of broken wires and/or internal corrosion including corrosion pitting.
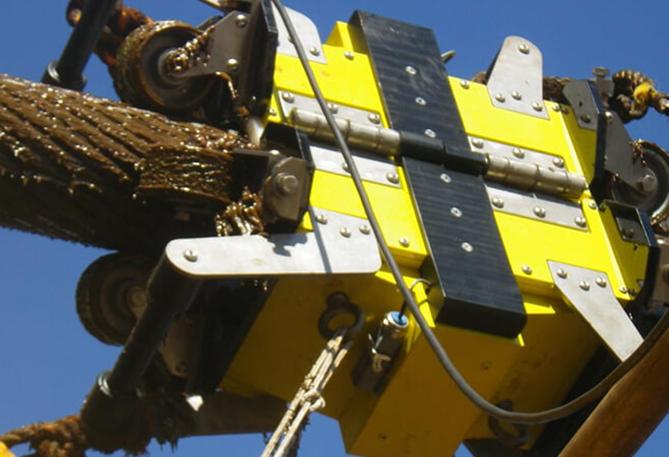
Failure of these ropes is frequently “unexpected” with no external indications of internal rope deterioration.
Our wire rope NDE instrumentation has the unique capability to reliably detect and quantitatively characterize (measure) these types of internal rope degradation.